In January 2016, Pi-Cubed Process Systems Ltd. was approached by the Client to help solve a unique problem regarding bitumen and asphaltene deposits on top of an internal floating roof (IFR) in one of their heavy oil blending tanks.
Several previous attempts had unsuccessfully been made to remove these deposits from the IFR resulting in concerns that the asset may be compromised and not be salvageable. During previous project scoping and execution, the Client had been unable to determine the absolute volume of this material or its composition.
Due to the uncertainties regarding the mass of the debris, the Client had taken a novel approach to estimating the volume of material on the IFR by carrying out stress analysis on the asset, resulting in an assumption that the roof would be able to sustain a maximum additional load of 220 tons of material. Based on this assumption, it was inferred that the correlating maximum volume of material on the IFR was less than 180 m3.
The Client looking to protect the asset from further damage and likely replacement contracted Pi-Cubed to develop an execution strategy for removal of the overburden on the IFR.
Material Properties
A sample of the material from the IFR was provided to Pi-Cubed for physical property analysis. Our laboratory analysis showed that the material had a high pour point and unless heat could be applied the material could not be mobilized through hydraulic means.
Dilution and mobilization experiments were carried out with several commonly available solvents and three (3) were deemed to be suitable for this project. Due to cost and availability within the refinery it was decided that light gasoline oil (LGO) would be used as a cutter stock for mobilization of the deposits on the IFR.
Implementation Strategy
In order to reduce the potential for damage should the IFR fail during processing and to accommodate heating from the fluid below the IFR the floating roof was lowered to just above the maintenance position. Heat was applied by recirculating heated fluid in the tank bottom using an external steam heating system. Further heat and agitation was then applied by heating the LGO cutter stock prior to driving the LGO under pressure into the accumulated material using automated nozzles mounted through the external fixed roof. The mobilized fluid consisting of cutter stock blended with the heavy hydrocarbon residue was then to be recirculated by drawing it off the IFR under vacuum and feeding it under pressure back to the nozzles.
During this recirculation process, the mobilized fluid density was predicted to change as additional heavy end product was mobilized from the tank floating roof. Our analysis concluded that a certain maximum fluid density would result in significantly reduced mobilization rates. Therefore, as the fluid density increased the cutting fluid was to be cycled out for new LGO, allowing the mobilization process to continue. The fluid removed from the tank was then to be re-introduced to the refinery for processing and sale.
Once the bulk of the material on the IFR had been mobilized, a final hot water rinse was to be applied through the automated nozzle system to remove surplus hydrocarbon from the floating roof and tank walls.
Cleaning Process Management
Under initial process parameters a steady heavy hydrocarbon harvest rate of between 20 and 30 m3 per day was achieved. The field team provided a rigorous data set of process parameters including density, temperature, flow and pressure. This data was then used as the basis for adjusting the system operating parameters to ensure the most efficient used of cutter stock and minimize tank downtime. Based on this data, Figure (1) shows clearly the recovery rate of material achieved.
Note, on the 5th day of automated processing, a significant reduction in harvest rate was observed. Further samples of the material showed a substantial change in physical properties. Analysis showed that the pour point of the material had increased by 5oC, likely due to preferential mobilization of the lighter hydrocarbons during the first five days of processing.
The reduction in harvest rate was overcome by increasing the recirculation system temperature by an additional 5oC. After two days of further heated recirculation, harvest rates were re-established and the recovery trend stabilised.
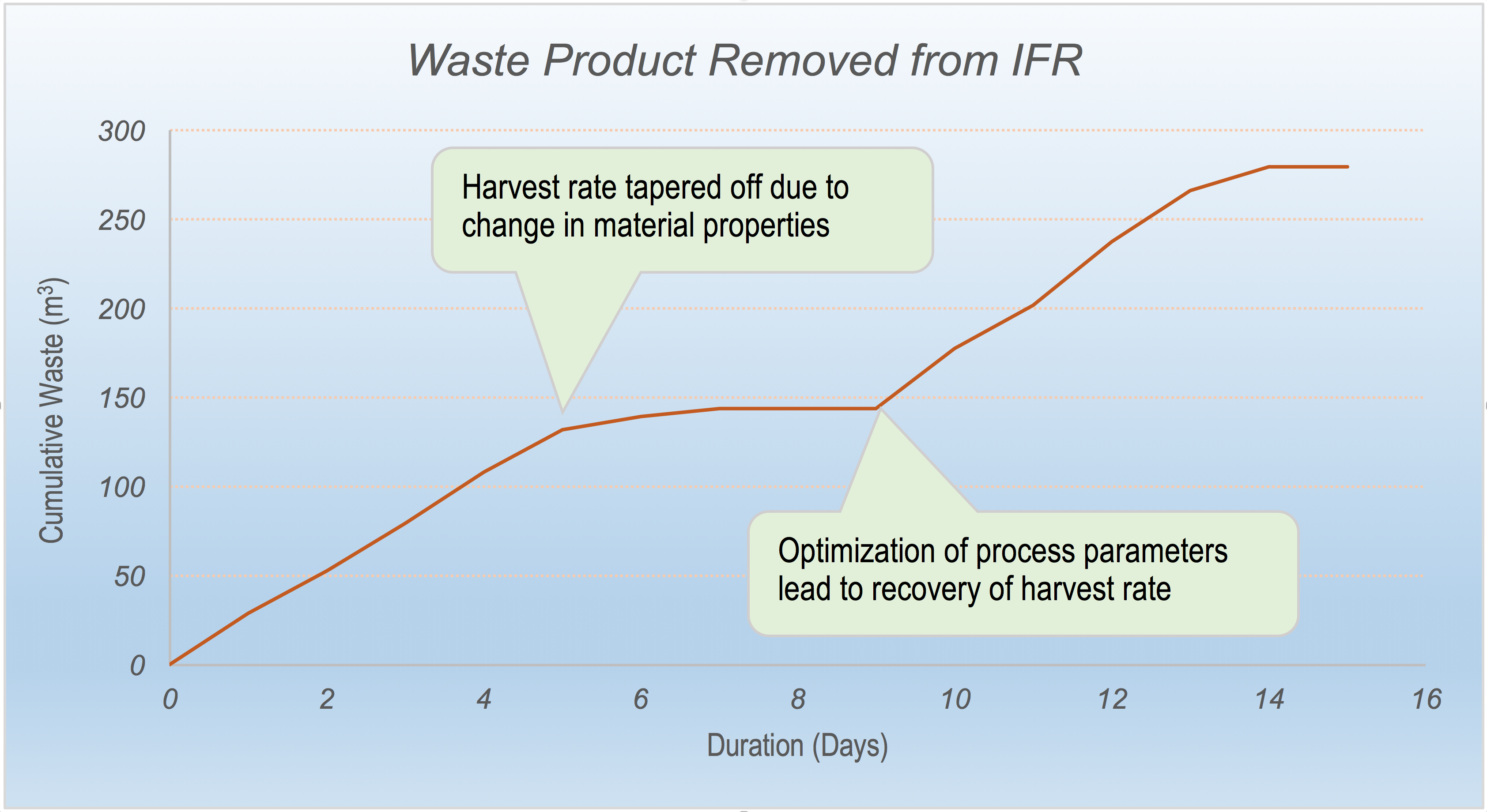
PiCubed crafts with technical
excellence and exceptional attention to detail.